Culture eats strategy for breakfast. This phrase is a popular catchphrase but still remains true. While workplace culture has become trendy, creating a safety culture remains a struggle. It’s the cornerstone of successfully implementing an effective health and safety program.
Safety culture refers to the mindset, attitudes, and behaviors of workers, supervisors, and owners toward safety in the workplace. It is impossible to fix it in isolation. You need coordinated efforts to create a wholesome safety culture.
It can be daunting to change your safety culture due to creeping complacency. Complacency can lead to catastrophic accidents, injuries, illness and sometimes threats to life. Don’t let this thought cripple you. There is always a way out.
Managers are not perfect. They can have limiting beliefs that prevent the effective implementation of a safety process. Be aware of the following roadblocks that can keep you from being effective:
Creating a Safety Culture
A systematic approach to creating a safety culture is the best way to start. Management needs to be on board and supportive of safe and healthy work practices. The goal is to instill new safety-related values in both management and staff. Remember the core responsibilities of both management and employees in an organization. These roles influence how they view the task of creating a safety culture. If you provide essential first aid kits and create safety training programs with these factors in mind, you’re likely to succeed.Management | Employees |
---|---|
Ensure inspection and adherence to safety regulations | Active participants in the workplace |
Leading by example by being role models of the safety culture | Responsible and accountable for their personal safety |
Organize and manage training | Prioritize safety when working as a team |
Hire safety professionals or assign safety tasks to employees | Adhere to the set rules and regulations |
Investigates incidents at the workplace | Notice and report safety concerns or ideas on the safety procedures |
Identifying and solving hazards |
Limiting Beliefs to a Safety Culture
There are mental roadblocks that prevent employees and management from immediately adopting safety. It’s important to be aware so you can know how to handle them. While management sets the pace for culture, both workers and leaders need to believe in the need for change. These common limiting beliefs offer insight into how to get support for a safety program.Employees
When an organization pays too much attention to processes and tools, it’s easy to forget the staff. This prevents employees from trusting their intentions. Underlying feelings are the greatest motivators of behavior. It is important to address these limiting beliefs before they show up and hinder safety in your workplace.-
Limiting Belief 1: Fear of Being Penalized
Despite their best intentions, many training programs leave employees wary of reporting incidents. They feel like they will be penalized for reporting too many incidents. They get this impression when procedures need staff to only report serious injuries. When employees hold back information, the whole company loses out. Management fails to learn from the near misses and other staff members don’t learn what to avoid. Frequent reports of danger are important in building an up-to-date safety policy. It will be able to accommodate changes in weather and unexpected challenges. -
Limiting Belief 2: Feeling Disengaged From Work
Employees feel disempowered when you enforce a safety rule that makes their work harder. They feel the same if you don’t consult or ask for their input. It’s discouraging when safety rules make work harder than necessary. To empower your staff is easy. When the safety team creates new rules, talk to your staff. Understand what they feel about the new regulations. They’ll give you insights you didn’t think of since they are on the frontlines. They have a better grasp of the implications of the rules. Managers can also try a policy called “Managed Safety” as opposed to “Regulated Safety.” “Managed safety” gives staff the leeway to wear protective clothing when it’s necessary. Strict compliance with rules is ‘regulated safety.’ It does little in ensuring safety standards improve. In environments with significant variations in operational conditions, “managed safety” is important. -
Limiting Belief 3: Valuing Productivity Over Safety
Since employees come to work to get things done, it is easy for them to sacrifice safety for productivity. Without a clear incentive to focus on safety, no one wants to be unproductive. Management needs to signal that safety is the priority. Otherwise, employees will conclude it’s okay to focus on results at the expense of safety. Management can counter this mindset by creating inclusive safety processes. Take work procedures into consideration while integrating safety and productivity. It sends a message that although work goes on, safety is the priority. It’s okay to pause work to solve safety issues.
Management
All levels of management serve as an example of safety culture in any organization. How they act toward staff and each other sets the tone in a company. When upper management supports workplace safety, it helps the employees embrace it.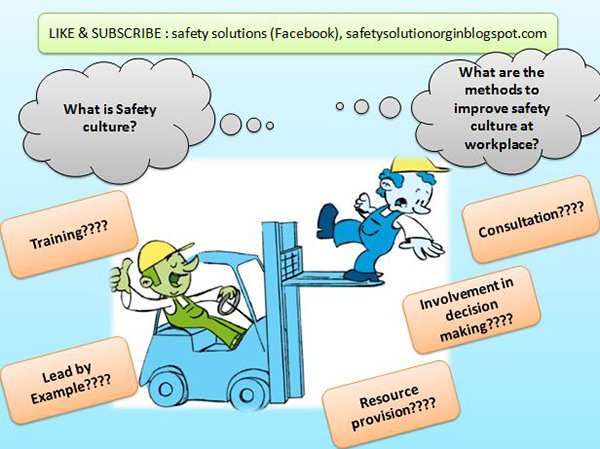
Sourec: safetysolutionorgin.blogspot.com
-
Limiting Belief 1: Negative Perspective on Culture Change
Half-hearted implementation happens when managers have a low expectation of the process They expect change to come in years if it ever comes at all. Some are passive while others come in with little to no expectations of change. When this happens, managers fail to gain support from key influencers, build momentum or deliver early wins. Managers shouldn’t wait to deliver bad news to a worker’s family to get serious about safety. Find a way to make it personal. This way, you can be able to spread the urgency of safety and cleanliness to your team. Change is possible in a few months of concentrated and deliberate effort. When you commit to creating change, nothing will stop you from implementing what needs to be done. Culture is intentional. When a manager is serious, the staff will know and fall in line. Simple things like increasing signage or safety posters can lead to a huge improvement in safety. -
Limiting Belief 2: Over-Reliance on Behaviour Incentives
In isolation, a behavior-based style of changing culture is defective. It leads to a culture of accusation where people get direct blame for accidents and incidents. Without considering external factors, you lose sight of reality. Well-rounded information helps you learn and put in place improvements. Reliance on behavior also leads to false incentive systems. When you reward workers for minimal accidents, it prevents staff from reporting all incidents. They do so to save their jobs and avoid penalties. This prevents your organization from learning about near misses and structural irregularities. Introduce structural cues that improve safety. They include signage in the appropriate areas. Place first aid kits strategically around your premises. First aid kits are crucial to a fast response in case of an accident. They are also a great psychological cue that reminds staff to value safety. -
Limiting Belief 3: Treating Safety as an Afterthought
Reactive safety management is a common problem. Managers focus only on what is measured. When your organization doesn’t reward managers for prioritizing safety, they will keep it as a low priority item. It’s natural to only focus on what will gain praise and a possible promotion. Most organizations use statistics like incident rates to measure safety. However, just because there are few injuries at the workplace, it doesn’t mean it is up to the appropriate standards. Change how you measure safety to ensure your workplace gets safer. Don’t expose your staff to unnecessary risk. A well-meaning manager can overlook safety if the wrong metrics are used to measure it. Measure safety through proactive action from both management and staff. When you keep track of what the team accomplishes, it makes safety a daily concern. This can include providing clean changing rooms for wearing protective clothing. Keep the workplace hygienic by providing lockers for both clean and soiled uniforms. Managing safety in addition to other duties can be daunting. Consider outsourcing a uniform and cleaning vendor that can save you the headache. Get one that suits your budget and needs.
Make Your Safety Culture Sustainable
Safety culture is a group effort that starts at the top and involves all employees. From the limiting beliefs explored, we realize they are a result of a miscommunication of priorities. Leadership needs to lead from the top. All levels of management are responsible for communicating the importance of safety. Lead with actions, and your team will soon be on board. Make it personal to become persuasive. For your employees, the key is consistent communication and engagement. They want to do a good job, and when you keep them in the loop, they feel a sense of ownership. An engaged employee is a productive employee. Work with reliable vendors to help manage the safety needs of your staff, and you can never go wrong.Photo: Fanjianhua